The Context
The current challenges in the manufacturing industry in Quebec are numerous and complex. Disruptions in the supply chain, whether orchestrated by external global events such as the pandemic, trade conflicts, or internal issues like logistical dilemmas, can trigger disruptions, shortages of raw materials, and potentially result in financial losses equivalent to 45% of the average annual profits of a company over the next decade.
Adding to this complexity is a workforce shortage affecting nearly 80% of Canadian manufacturing companies, creating a challenging mix of issues.
In the face of these challenges, innovative solutions need to be implemented.
AI and Generative AI as a Solution?
Artificial intelligence is employed by manufacturing companies for its ability to optimize manufacturing operations, increase worker productivity, reduce costs, and improve customer satisfaction.
Generative AI can also play a dominant role in the manufacturing sector at a lower cost, faster, and without requiring as much data as “traditional” artificial intelligence projects. It is also a style of solution that is typically better embraced by workers impacted by these changes, thanks to a user experience that promotes collaboration and reduces the need for deep AI knowledge.
Indeed, generative artificial intelligence is accessible because it is possible to quickly test a solution with a proof of concept, without the need for pre-existing data or advanced programming skills.
Thanks to its ability to process vast amounts of data and generate intelligent responses, generative AI can transform maintenance workflows, solve problems in real-time, recommend ways to improve production line efficiency, and become an indispensable tool for fostering the design of new products!
According to the Google Cloud Gen AI Benchmarking Study of July 2023, 82% of organizations considering or currently using generative AI believe that it will bring significant changes, even a radical transformation to their industry.
Series on generative artificial intelligence
- The Essential Use Cases of Generative Artificial Intelligence
- Why you should use ChatGPT in a business context
- How to leverage generative artificial intelligence solutions in business without drifting [Conference on demand]
- Automated Generation of Metadata: Solutions for SAP, Oracle, and Microsoft Dynamics Inventories
Generative AI is Not Just a Decision Support Tool
While most people know generative AI as ChatGPT, Gemini, or Midjourney as a “generic” assistant, it is possible to deploy generative AI in a more specific manner to exploit opportunities and solve particular problems.
Naturally, using the input bar, we can dictate our commands (prompts) to get answers. However, with the same technology, it is also conceivable to program it to solve targeted problems.
Generative AI System for General vs. Narrow Purposes
Generative AI System for General Purposes: An example of this type of system is ChatGPT, where the user receives a textual response based on their query. The user can provide information related to any task they want to accomplish and receive a response tailored to the scope of their question.
Generative AI System for Narrow Purposes: In the manufacturing domain, a concrete example of such a system would be a generative model specifically designed to optimize the production planning process. Rather than simply answering general questions, this system would be trained to analyze specific production chain data, such as stock levels, supplier delivery times, and customer demands.
For example, a production manager could use this system by providing information about current orders, current production capacities, and resource constraints. In return, the system could generate proposals for optimized production plans, taking into account deadlines, costs, and available resources.
Thus, this narrowly specialized generative AI model would be capable of providing precise and targeted solutions to improve operational efficiency in the manufacturing context, going beyond the generic functions of general AI systems like ChatGPT, Gemini, or Midjourney.
Practical Applications of Generative AI in the Manufacturing Industry
Here is how generative AI is used to create value in the manufacturing industry.
6 Use Cases of Generative AI in the Manufacturing Industry
The revolution of generative AI is that it uses YOUR data, YOUR ways of doing things.
One of the risks of using general-purpose generative AI solutions is receiving a response that is not truthful or personalized to our context. Asking ChatGPT to generate a quote for a manufacturing plant is possible, but each company has its own identity, methods, processes, and brand tone. These are important elements to consider. It would be far-fetched to assume that all manufacturing companies are identical!
What will truly revolutionize your approach with generative AI is considering YOUR own database. By making your company’s data available in a secure environment, it allows your “Enterprise GPT” to understand your reality and the format of historical submissions, thus generating a result faithful to your methods. Moreover, when talking about databases, it can be any data, whether structured or simple web pages containing useful information.
In the manufacturing sector, this approach allows companies to fully leverage their own data, such as historical data, past submissions, tender documents, production plans, and engineering plans. By using these resources specific to each company, generative AI shapes customized solutions in the image of the company itself, often rivaling (and often surpassing) the quality obtained through manual processes. It is a capitalization on accumulated expertise over time, paving the way for rapid and extremely effective innovation.
With a generative AI solution based on your data, you can (among other things):
- Instantly generate a new quote for a new client, with new parameters, but based on your past submissions.
- Create new project plans based on your historical plans.
- Respond to tenders based on your past responses and your way of responding to tenders.
- etc.
1. Automation of Customer Service
Conversational agents, also known as chatbots, which are increasingly powered by generative AI, offer a natural and seamless interaction with users while adhering to internal governance policies and brand image. Capable of generating relevant and consistent responses to posed questions, chatbots significantly improve user experience and customer service efficiency.
In the manufacturing sector, companies leverage these conversational agents to facilitate product troubleshooting, order spare parts, schedule services, and provide information about products and their operation.
Manufacturers and industrialists can also benefit from internal conversational agents, assisting employees in quickly searching and retrieving information from vast databases, including their own internal database. Employees can interact naturally with these agents to ask complex questions and get relevant answers, facilitating decision-making and access to internal knowledge.
Imagine equipping your colleagues with virtual and instant assistants that provide answers to challenging questions about the operations or maintenance of your machines and equipment, or assist your engineers in drafting documents that must comply with the numerous standards your company must juggle.
2. Research, Synthesis, and Document Production
Generative AI excels in text understanding and can greatly aid in the synthesis, modification, and creation of text through in-depth research of internal documents from various sources.
A mechanic in the manufacturing sector can benefit from the technology to have a summary of maintenance instructions in seconds, saving repair time and ultimately returning to production more quickly.
Moreover, an engineer can use this technology to generate instruction manuals and documentation for factory machines or accompanying finished products.
Here’s what this means for manufacturing companies.
Internal Chatbot for Employees: Deploying an internal chatbot to help employees quickly access internal information and procedures, which can improve operational efficiency.
Manufacturing Data Analysis: Analyzing production data and identifying trends, inefficiencies, or anomalies, thus contributing to the optimization of manufacturing processes.
Support for Technical Experts: Generating summaries of complex engineering reports, patents, and research documents to help engineers and technical experts stay abreast of the latest industry developments.
360-Degree View of Customers in Manufacturing: Centralizing customer data to have a comprehensive view of their needs, interactions, and histories, which can improve product and service personalization.
Feedback Analysis: Summarizing customer or employee reviews and feedback to identify recurring issues, possible improvements, and positive feedback, which can help improve product quality and production.
Customer Segmentation: Using AI to segment customers based on their purchase history, preferences, and needs, which can help personalize offers and marketing campaigns.
3. Generative AI to Accelerate Prototyping
One of the main contributions of generative AI lies in its ability to create. One crucial advantage is its ability to speed up the design process.
Traditionally, prototyping is a laborious and time-consuming process involving many iterations. Generative AI, on the other hand, can propose ideas and quickly generate prototypes, reducing the time needed to move from the design phase to the production phase.
This acceleration of the development cycle allows companies to respond more quickly to market demands and remain competitive in a constantly evolving business environment.
In terms of costs, generative AI offers significant advantages. By automating part of the design process, companies can reduce labor and prototype iteration costs. Moreover, AI’s ability to optimize materials and structures can lead to substantial long-term savings on production costs.
Imagine being able to generate 3D plans more quickly, receive suggestions on the best packaging for a given product, or automatically generate a design that adheres to the customer’s color scheme.
4. Advisor in Supply Chain, Continuous Improvement, and Legal Documents
Generative AI positions itself as a strategic guide within supply chains, broadening the perspective within complex networks and issuing recommendations for the most suitable suppliers based on relevant criteria. These criteria encompass not only detailed specifications of bills of materials but also parameters such as raw material availability, delivery deadlines, and sustainability indicators.
Endowed with a particular skill in natural language analysis, generative AI excels in extracting relevant provisions from legal and contractual documents. This ability to decipher the ins and outs of legal agreements allows generative AI to play an essential role in the continuous improvement of operations, thereby strengthening the overall efficiency of the supply chain.
5. Generative AI in Predictive Maintenance
AI is already well-utilized in predictive maintenance with forecasting. Let’s take an example in the aerospace industry. Pratt & Whitney uses an artificial intelligence model that predicts the maintenance schedule for a given engine. By cross-referencing these activities with P&WC’s clients, a prioritized list of customers to contact is produced for their sales team.
Generative AI, on the other hand, distinguishes itself by its ability to not only suggest potential solutions when identifying a problem but also to proactively develop comprehensive service plans.
In this context, consider a scenario where a problem is detected. Generative AI steps in not only to provide solution suggestions but also to develop a detailed plan guiding maintenance teams through the entire resolution process, all using your data and guidelines.
A key feature of this technology is its increased accessibility to manufacturing engineers. They can interact intuitively with AI, using natural language and common queries. This ease of use makes generative AI not only accessible to the existing workforce but also particularly attractive to new employees, thus opening up new perspectives in the field of predictive maintenance in the manufacturing sector. Here’s a video produced by Google demonstrating how generative AI helps a transport company solve a problem with a defective locomotive.
6. Metadata Generation for ERPs
For new products, AI automatically generates descriptions based on similar products in inventory or brief information provided by the user. The generative AI system can be integrated into SAP, Oracle, or Microsoft Dynamics. This can be achieved through API integrations or custom modules, ensuring that the generated metadata seamlessly integrates into the raw material and stock management system.
This innovation simplifies and streamlines inventory management, allowing teams to focus on higher-value tasks and accelerate the launch of new products.
I present in this article a demonstration of how metadata generation works from text and from an image.
Implementation of Generative AI in the Manufacturing Industry
To successfully integrate generative AI, operations and innovation managers must follow crucial steps, including selecting appropriate partners and tools, developing a robust and functional solution, training staff and managing change, and implementing a long-term strategy to maximize the benefits of generative AI. Here’s a link to an ebook that guides managers in their first AI project.
In summary, generative AI represents an unprecedented opportunity for the Quebec manufacturing industry. In a constantly evolving industrial landscape, the adoption of generative AI represents a bold step towards efficiency, innovation, and competitiveness. By following these emerging trends, the manufacturing industry in Quebec can not only overcome current challenges but also thrive in a technologically advanced future.
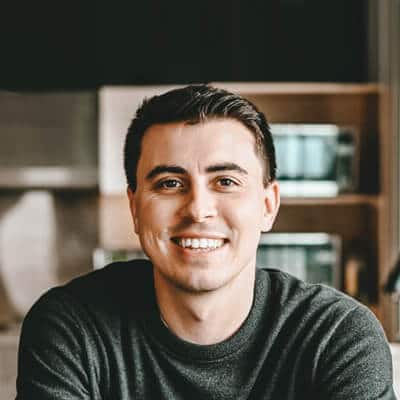
Olivier is co-founder and VP of decision science at Moov AI. He is the editor of the international ISO standard that defines the quality of artificial intelligence systems, where he leads a team of 50 AI professionals from around the world. His cutting-edge AI and machine learning knowledge have led him to implement a data culture in various industries.